Join us at AREMA, Indianapolis – Sept 14-17
General Info
Limits Compliance & Collision Avoidance System.
Piper Helix™ is an advanced, multi-sensor Limits Compliance and Collision Avoidance System (LCCAS) that integrates LiDAR, UWB and other technologies.
The Maintenance of Way (MoW) safety solution allows for fleets of rail-bound and hi-rail equipment to be accurately detected and tracked on the railroad in real- time, thereby reducing the potential for worker injury, equipment damage, and operational disruptions resulting from accidents or major rule violations. The system addresses several challenges that transit agencies and freight railroad’s face today, including: Limits Compliance, Collision Avoidance, Object and Worker Detection, and Collision Detection. In addition to providing this vast array of operational information to MOW vehicle operators, Piper also consolidates information for foremen and employees-in-charge who are assigned multiple vehicles from the work gang. Foreman tablets provide interfaces to monitor vehicle locations and onboard telemetry in real-time.
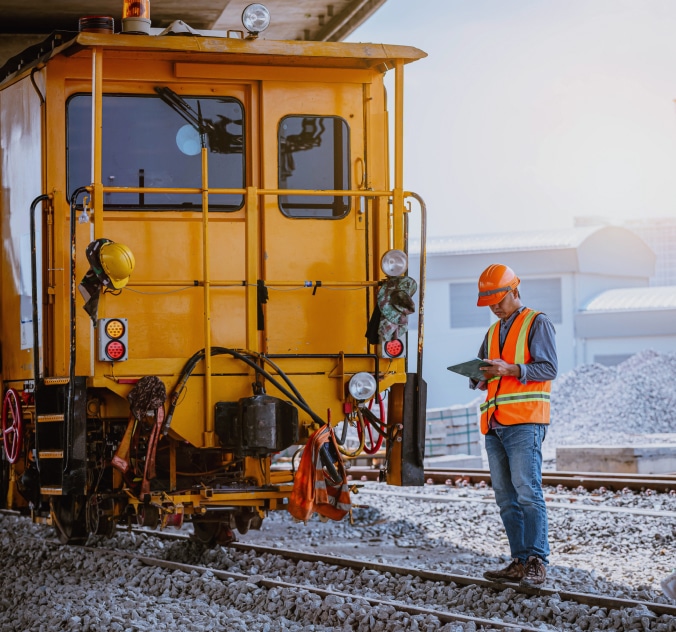
Maintenance of Way Safety Solutions
Limits Compliance
01Limits compliance functionality relies on Piper’s GPS RTK technology to position MOW vehicles in the territory with centimeter-level accuracy.
This accuracy is critical for determining the track the vehicle is operating on and calculating the distance to the ends of the work zone. To accomplish this, Piper deploys redundant, broad coverage GPS-RTK base stations along the right of way.
Piper recently deployed a comprehensive database of the entire Northeast Corridor track geometry and required only 32 base stations.In addition to determining precise track and location, this network provides fine resolution for the proximity of vehicles to various points of interest, including: interlockings, platforms, grade crossings and signals.
Piper GPS RTK base stations provide incredible centimeter level accuracy. Only 32 devices total were required to cover the entire NEC making it a cost effective and fast installation.
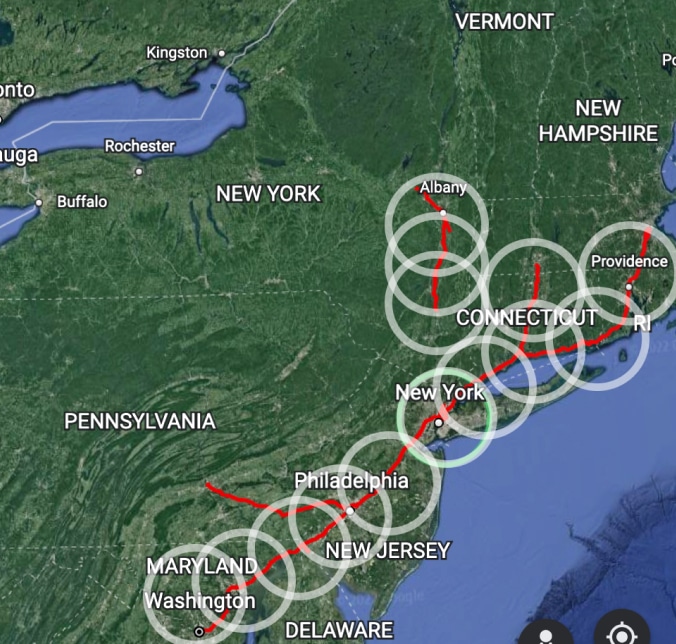
Collision Avoidance
02Work zones often include multiple MoW vehicles operating in close proximity to each other with bi-directional movements.
It’s imperative to monitor the front and rear of each of these vehicles to prevent collisions and damage. For this function Piper deploys its field-tested UWB solution. The Helix CPU uses its knowledge of which track the vehicle is localized to and communicates with other Helix-equipped vehicles on the same track using UWB in a localized fashion. The ranging data collected from the UWB sensors allows the Helix CPU to accurately track the distance between the two vehicles and warn both operators if they begin to encroach on their safety envelopes. Operators are able to view this proximity information through the in-cab display alerts that follow the rules for safe separation of vehicles in both work and travel modes.
Piper’s UWB technology became the world’s first SIL 4 safety certified UWB positioning system.
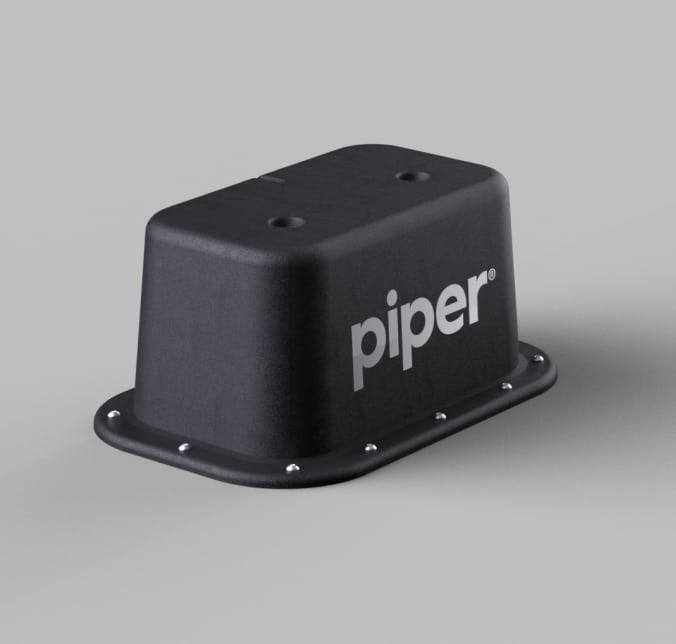
Object and Worker Detection
03Operators are also alerted to the presence of workers that inadvertently cross the track fouling area as well as objects that may be left in the path of the vehicles.
Piper’s TrackSight™ LiDAR system is calibrated to focus its field of view towards the direction of the track for the purpose of detecting any obstacles which could result in a collision with the operating vehicle. The sensor is configured to ignore any observed objects which don’t meet the minimum threshold for size as to avoid false positives caused by common debris. Additionally, TrackSight™ can determine its distance to observed objects and notify the equipment operator of when they should prepare to stop based on their current speed. The system also takes into account the database residing on the local CPU to dynamically focus its field of view when the vehicle is approaching a curve or the track is changing elevations.
According to the FRA, there were over 3,200 train-related injuries for on-duty railway workers in 2021.
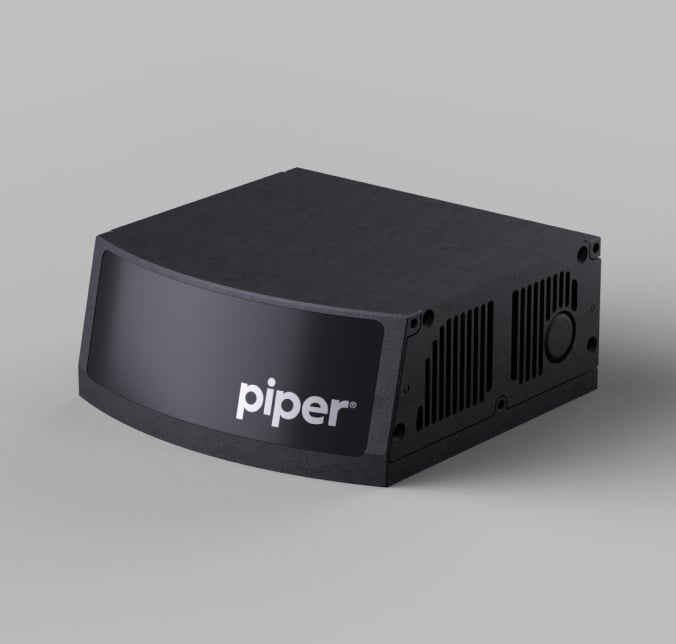
Collision Detection and HD Cameras
04Inertial Measurement Units (IMU) detect collisions in real-time and HD Cameras store outward and inward recordings for forensic review following hazardous events.
The Helix IMU includes a digital signal processor called Motion Processor which fuses acceleration and gyroscope data. The Accelerometer measures physical acceleration while the gyroscope measures angular/rotational velocity. Piper’s IMU accelerometer measures acceleration in meters per second squared which Piper then converts each acceleration into a g-force measurement to give the LCCAS system an understanding of any collisions which have occurred on the local asset. While the TrackSight and UWB sensors will enable the Helix system to alert the vehicle operator, EIC, and Dispatcher when a collision is imminent, the IMU will enable Helix to immediately alert the EIC and dispatcher when a collision occurs.
Additionally, the IMU gives the Piper LCCAS system the added function of dead reckoning for enhanced availability.
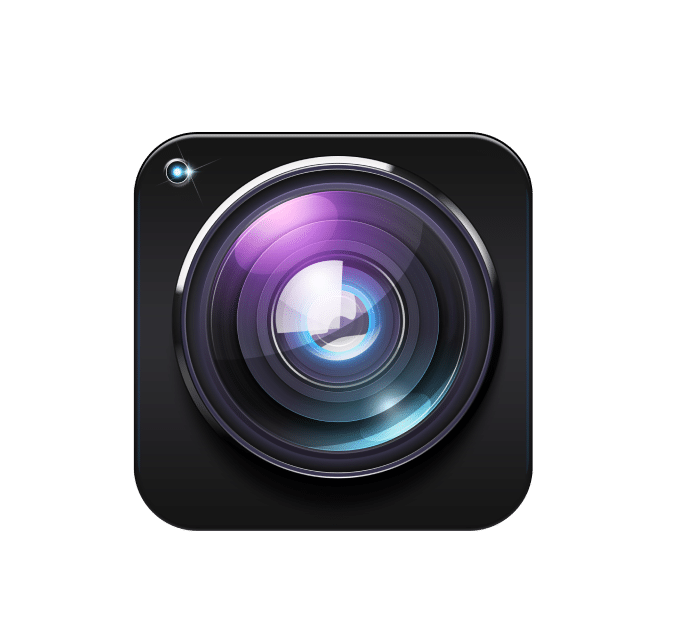
Virtual Tunnels
05In order to reduce alert fatigue, Piper uses advanced algorithms that create Virtual Tunnels.
Using the database created from the Virtual Tunnels, Piper distinguishes between objects that are breaching the fouling area or creating a hazard, from necessary and existing wayside infrastructure such as signal heads or gantrys.
To eliminate false positives, the TrackSight sensor takes into account the database residing on the local CPU to then dynamically focus its field of view when the vehicle is approaching a curve or the track is changing elevations.
Piper has developed innovative algorithms to prevent false positive obstacle alerts when vehicles approach curves and hills.
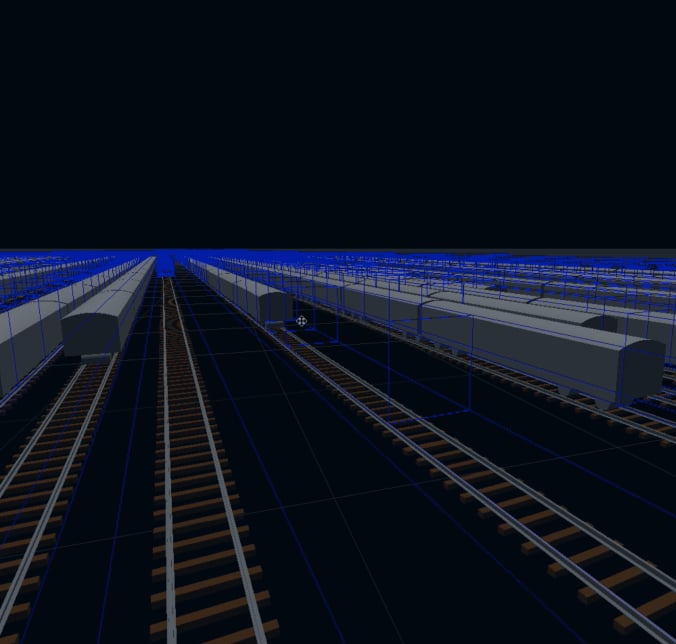
Piper Helix Overview
Testimonials
Proven in the field
Benefits
Benefits that make a difference
High Precision
Reliable System provides accurate navigation for rail vehicles.
Works in extreme conditions
& above or underground rail environments.
Advanced protection
For MOW equipment and track workers.
Suite of sensor technologies
includes UWB, LiDAR, IMU and optional GPS.
Consistent two-way communication
with local MoW system using LTE Modem.
SIL 4 Safety Certified Equipment
tested against AREMA C&S 11.5.1 and IEEE 1478
Piper’s news
Other Solutions
Reliably Innovative Transit Solutions
Piper has an existing suite of real-time location systems (RTLS) solutions that utilize various technologies, including: UWB, BLE, GPS-RTK, LTE, RFID, HD Cameras and LiDAR.
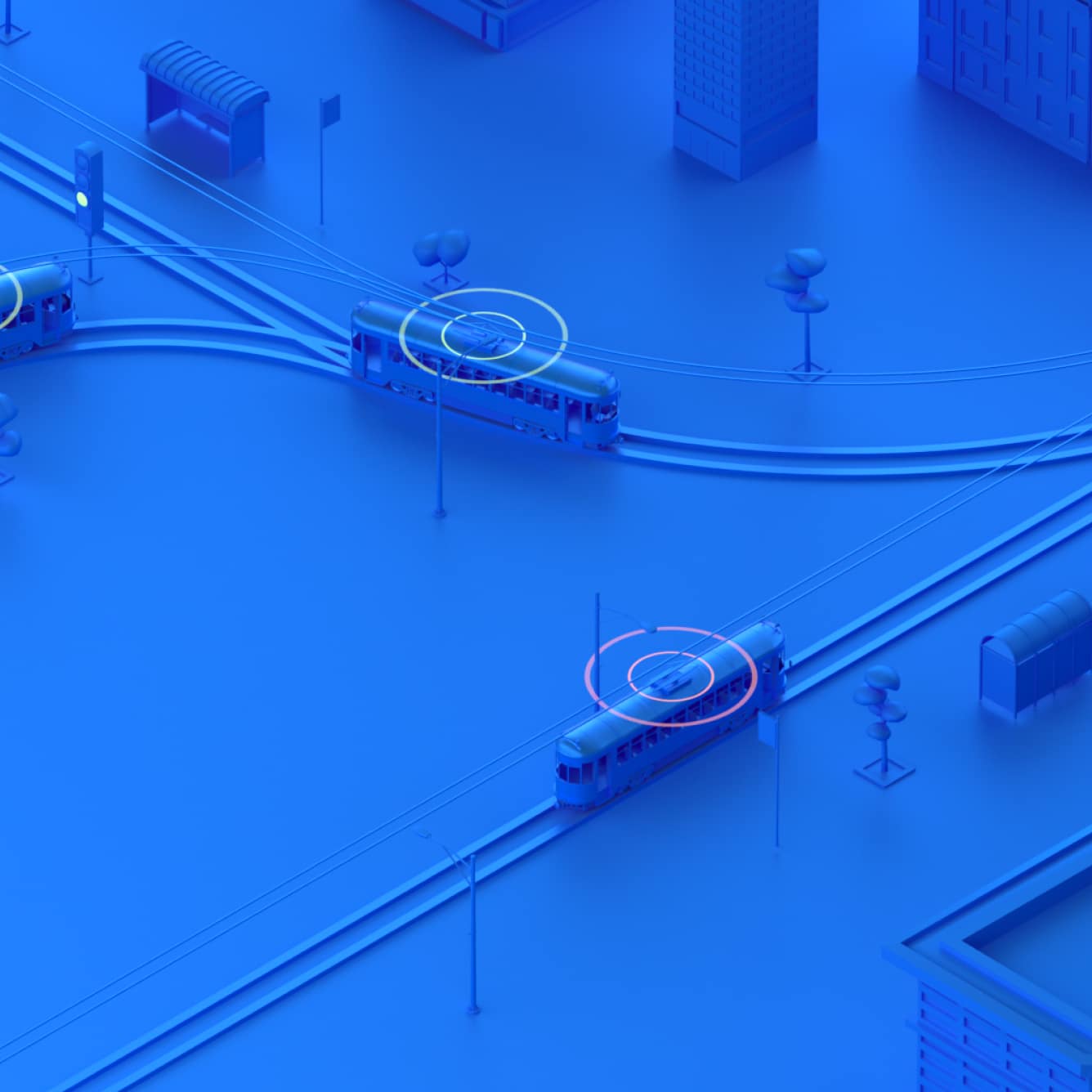
ATP-Overlay
Automatic Train Protection for localization, safe separation, rollback protection, end-of-train, and more.
Learn more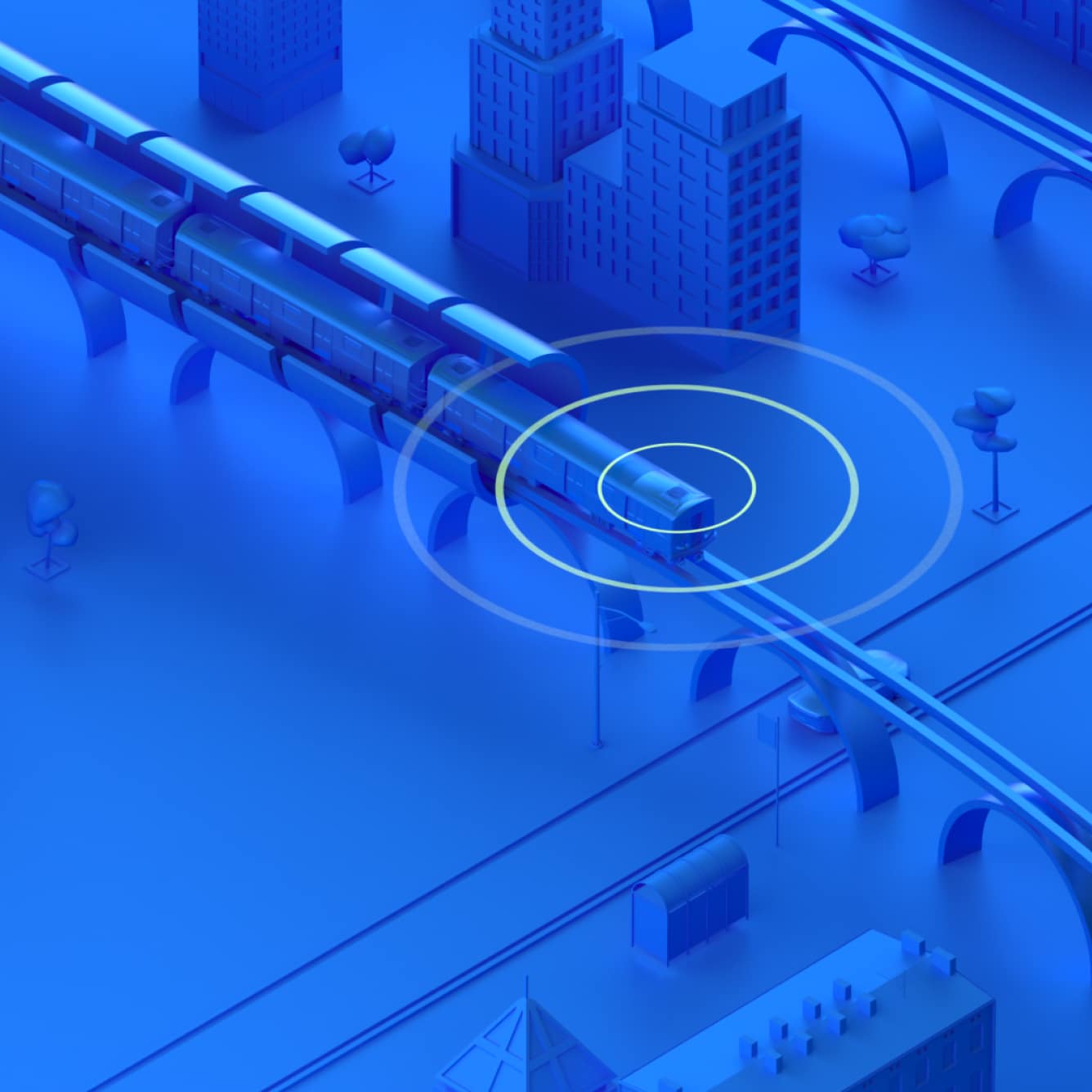
Train Navigation
Determine the location of trains with unmatched positional certainty, even underground or on elevated tracks in the city.
Learn more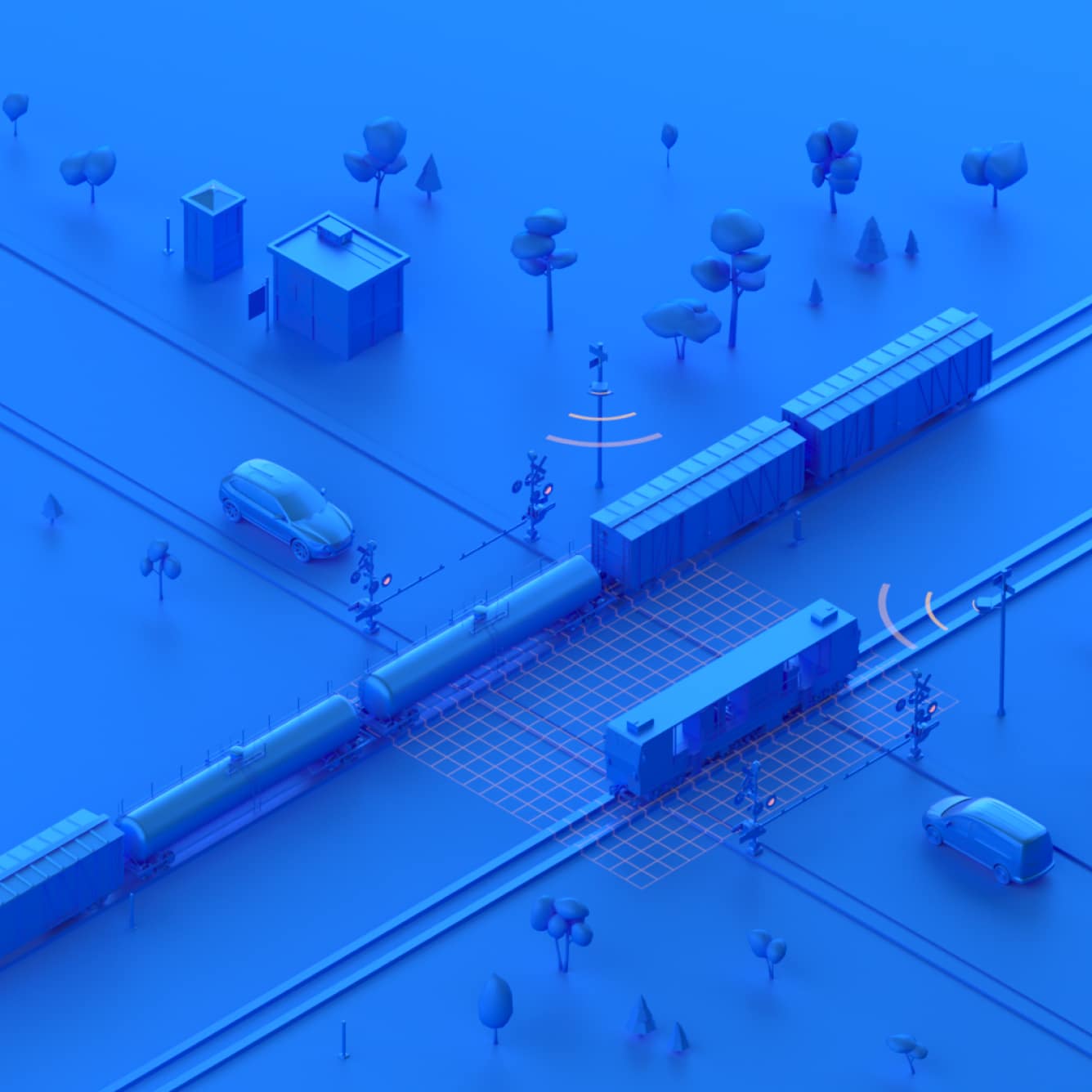
Grade Crossing Safety
Monitor grade crossings remotely to detect occupancy and alert rail system operators to potential hazards.
Learn moreOur single platform is not only designed to communicate seamlessly with your existing systems, but they can also be interoperable with your legacy equipment. Use Piper’s proven solutions to improve efficiencies and safety, or contact us to develop something specific to your requirements.
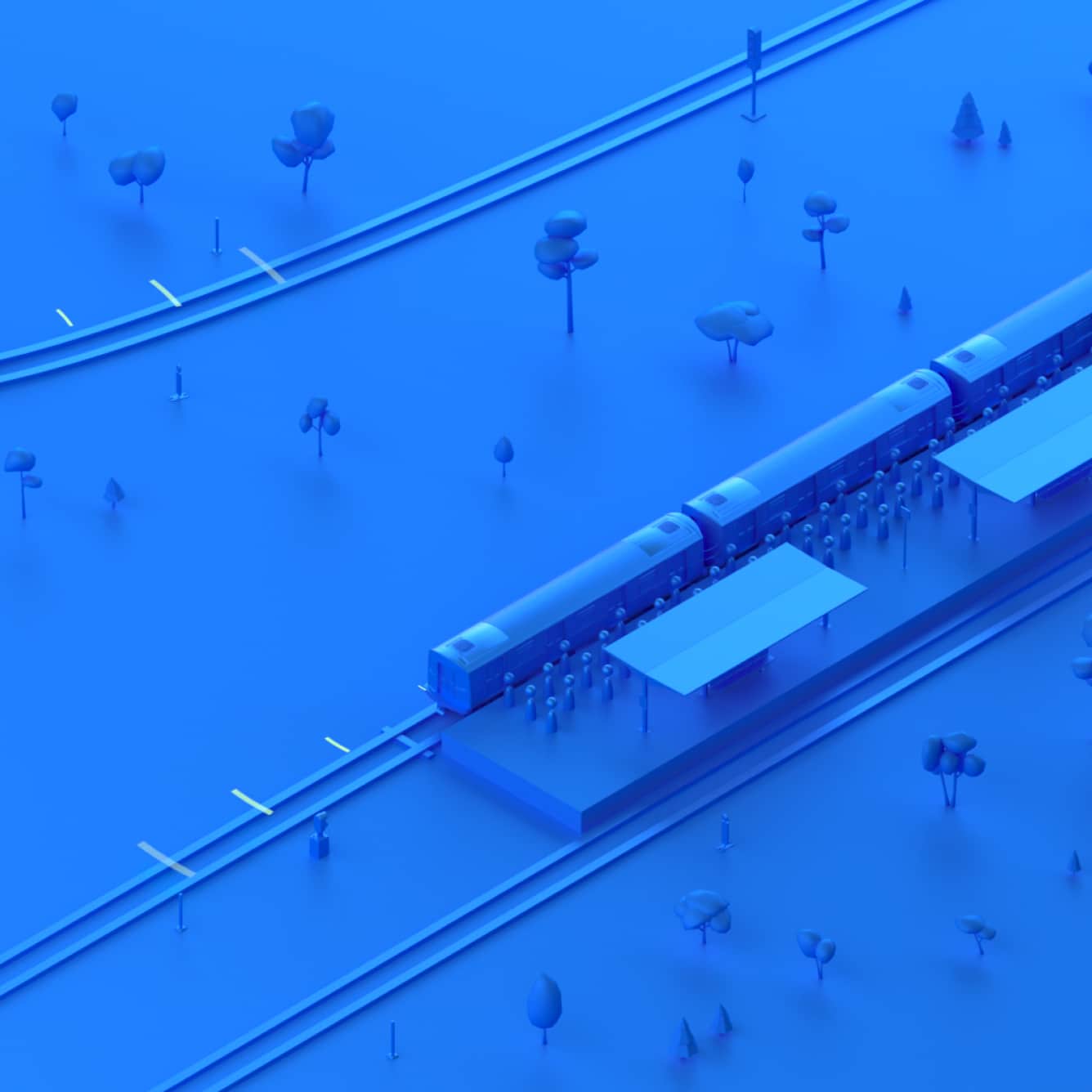
Station Safety & PIDS
Calculate train arrival/departure times to improve rider experience, and keep them safe on the platforms with special track intrusion cameras.
Learn more